Project Efesto
Context: New Space Economy
The potential of Space 4.0 exploration for Italy, Europe and the world is enormous. Europe and the world are facing major global challenges which require equally global responses and imply responsibilities.
According to ESA definitions, Space 4.0 era is a time when space is evolving from being the preserve of the governments of a few Spacefaring nations to a situation in which there is an increased number of diverse space actors around the world, including the emergence of private companies, participation with academia, industry and citizens, digitisation, and global interaction.
Objective: Improve the Italian heritage of Liquid Rocket Engines
Project Efesto aims to contribute in a strategic, dynamic, and innovative way to the New Space Economy, playing a role in the European mission: to shape the development of Italy’s space capability, and ensure that investment in space continues to deliver benefits to the citizens of Europe
Liquid propulsion is a relatively new concept for Italy, originated thanks to AVIO's M10 engine development. In order to provide support to the Italian liquid rocket engine initiative, Polito Rocket Team's Project Efesto is developing the first Italian pressure-fed Liquid Rocket Engine.
Characteristics
Reusability
Liquid rocket engines are known as one-mission engines. Nowadays, to reduce space pollution and cost per kg to orbit, important industries are focusing on the reusability of the first rocket stages. To pursue this goal, liquid rocket propulsion is one of the key factors.
PoliTo Rocket Team has chosen to fully develop a regenerative liquid rocket engine, in order to propose a small and reusable propulsion system for the first stages of a general micro launcher.
New technologies
Nowadays, manufacturing processes are playing an important role in the global space industry, with a particular emphasis for space propulsion.
The Liquid Propulsion Project aims to produce the whole engine assembly via additive manufacturing. Thanks to this process, new geometries and potential mass optimization can be investigated, leading to novel design opportunities, cost reductions, and technological advancements.
New Materials
The thrust chamber of a high-performance bi-propellant liquid rocket engine is a critical component of the launch vehicle because it is designed to operate in some of the most severe conditions seen in engineering practice.
The requirement of reducing the temperature of the walls exposed to the hot gas can be met with high-thermal conductivity copper alloys, while mechanical stiffness is achieved by using high-strength steel or nickel alloys.
Because the stress-strain behavior of a regeneratively-cooled thrust chamber is directly correlated with its temperature behavior, it is of primary importance to select the correct alloys.
Thanks to the Politecnico R&D partnership, the Efesto Engine will be designed with some of the most recent copper-based metal matrix composite materials.
Static fire qualification program
The Efesto engine under development is being designed to be tested with a new test bench facility. Qualifications and integrations will be performed to meet mission requirements and targets
Simplicity
The regenerative pressure-fed engine cycle can provide great results with more straightforward design efforts in comparison to more complex engine cycles, such as e-pump-fed or open engine cycles
Specs
Oxidizer | Fuel | Cycle | Targer Thrust |
---|---|---|---|
Nitrous Oxide (N2O) | Ethanol | Pressure-fed | 5 kN |
Systems
The purpose of the Efesto project is to develop the liquid system needed for the first bi-liquid project of PoliTo Rocket Team. The project is working on 5 different lines:
TCA | Thrust Chambe Assembly |
---|---|
EC | Engine Cycle |
LSA | Liquid System Architecture |
TB | Test Bench |
ECS | Engine Control Strategy |
Thrust Chamber Assembly
The Thrust Chamber Assembly (TCA) division is responsible for the development of the components of the thrust chamber. Innovative additive manufacturing techniques allow us to push the limits of manufacturing in order to improve performances and reduce costs. The actual design of the engine includes two main components, the injector head and the combustion chamber, joined by a bolted connection. The design of the injector head has been presented at the 26th ESA PAC Symposium on European Rocket and Balloon Programmes and Related Research in Luzern on May 2024
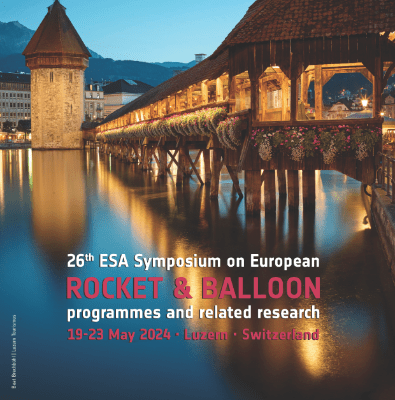
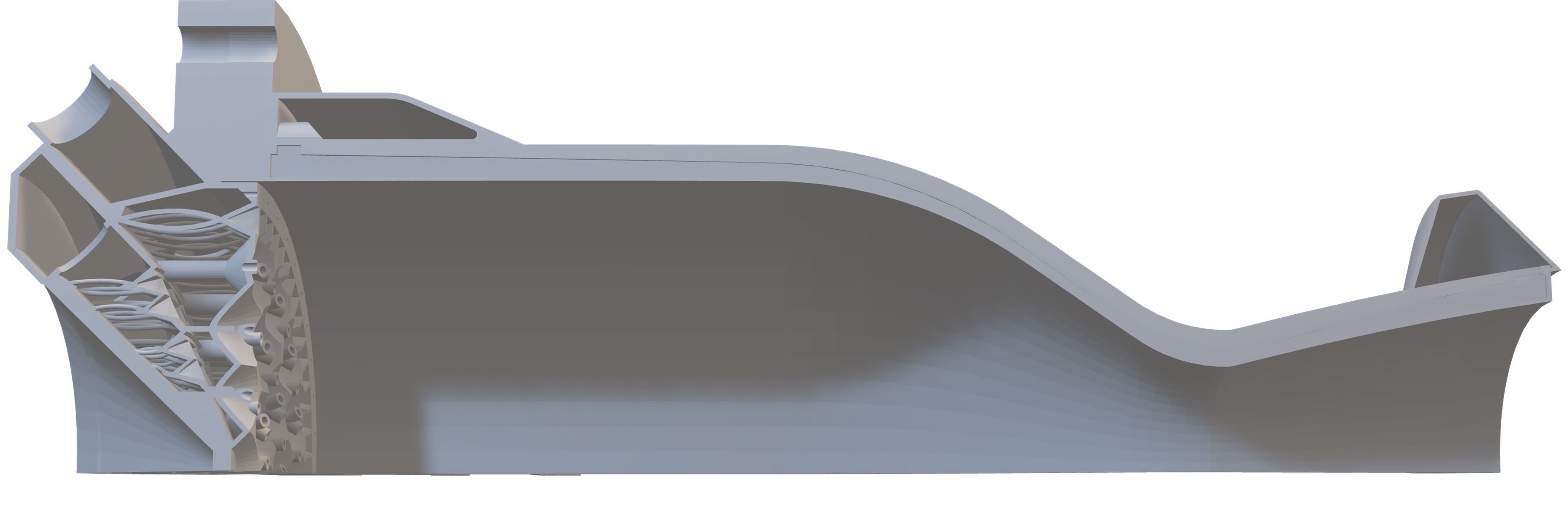
Engine Cycle
The engine cycle division is developing a proprietary tool, named RocketForge, to manage all the engine aspects. An in-house calibrated software is essential in order to fast improve with the engine design and to quickly provide new reliable engine configurations. The division is also responsible for the engine cycle definition and for the support to the test data processing.
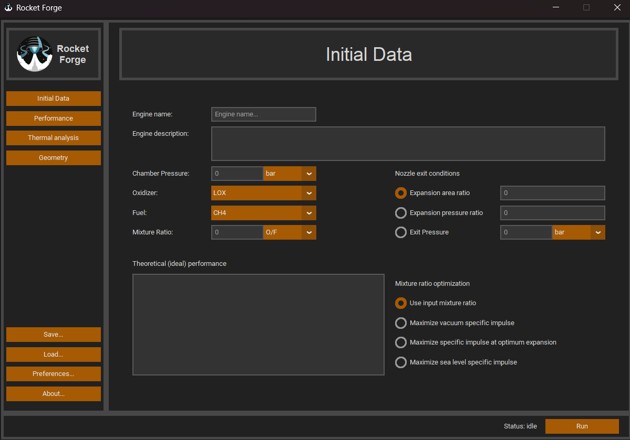
Engine Control Strategy
Power is nothing without control, therefore the ECS division works on the development of the hardware/software system to control the valves and obtain the sensor readings needed to precisely control the valve system.